Shimanto, located in the Shikoku region, is 87% forest. One of our local products is hinoki cypress.
The resulting design is like a hall of fame to hinoki cypress, which is in ample supply due to forest thinning efforts.
The prideworthy local brand of hinoki cypress was used symbolically in the Shimanto town hall and leaves a lasting impact on those who see and visit the space.
The finished product is a testament to the pride locals feel for this lumber.
It would be no exaggeration to call it a “hall of fame” to lumber. The external walls at the front are all made of joined planks of Shimanto hinoki. Shimanto hinoki is a local “brand” that we are proud of. Now, this famous local product has taken new form as a government office, an edifice that will be visible to all. It has literally given form to the pride and joy of locals. Every time I come to work here and see the building, I am revitalized. I feel like I have to do my best work to live up to this building’s greatness. (laughs) Now we have another lovely landmark in town. Hinoki cypress is used for the floor, walls, and ceiling. You get to engage with the warmth of wood up close while you work. Both visitors to the office and workers alike find the space pleasant and inviting. Town halls and government offices used to be emblems of authority and influence. Or, they would take the opposite approach, and eschew all ornamentation to appear stoic and bland. It’s hard to get away from that feeling of going to the town hall and finding it cold and unapproachable. We wanted to make the town hall a more inviting and important part of people’s lives, which is why we opted for this warmer look.
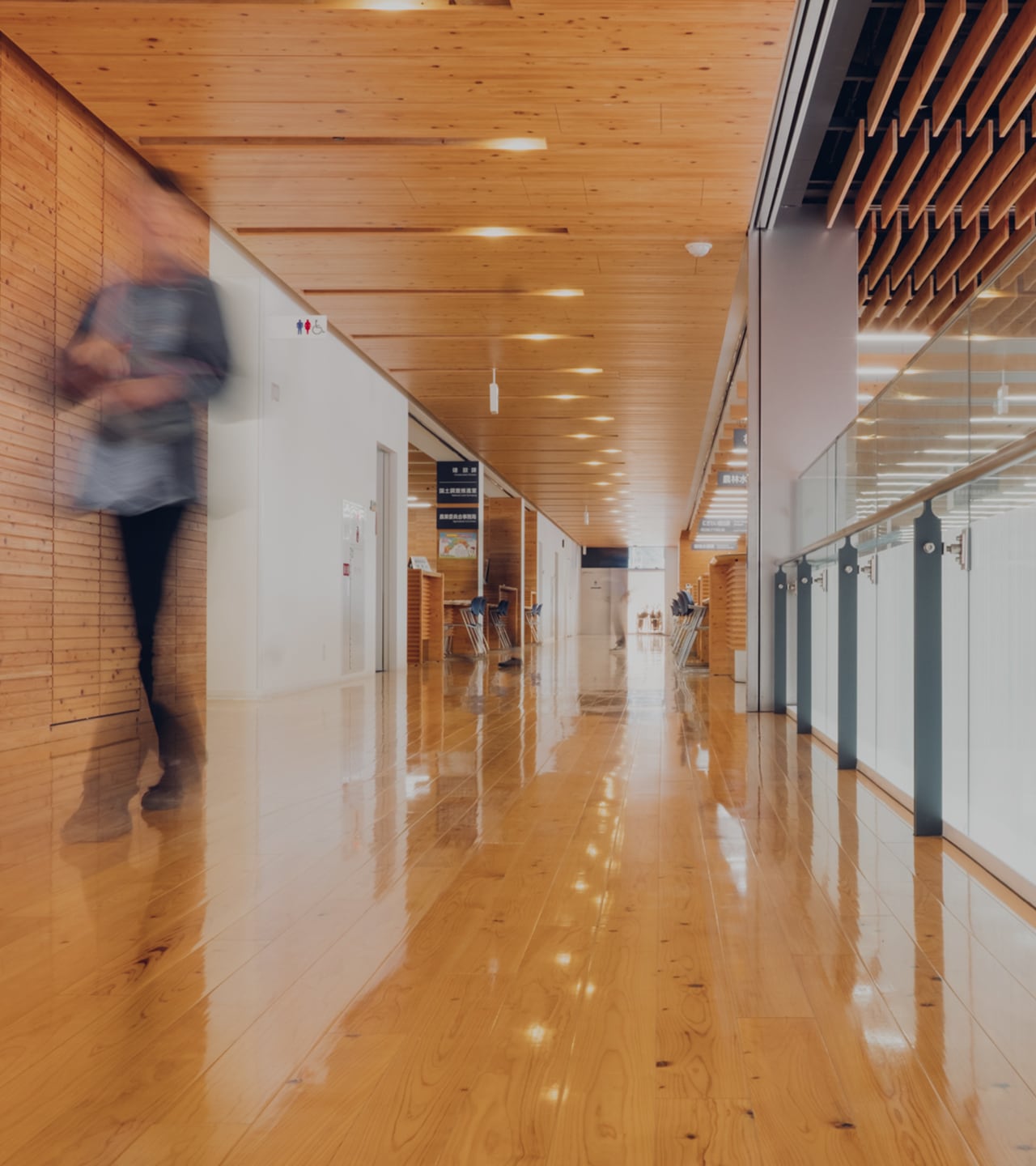
Giving shape to locals’ pride
The Shimanto town hall went from a bland building to a warm and inviting “hall of fame” for hinoki cypress.
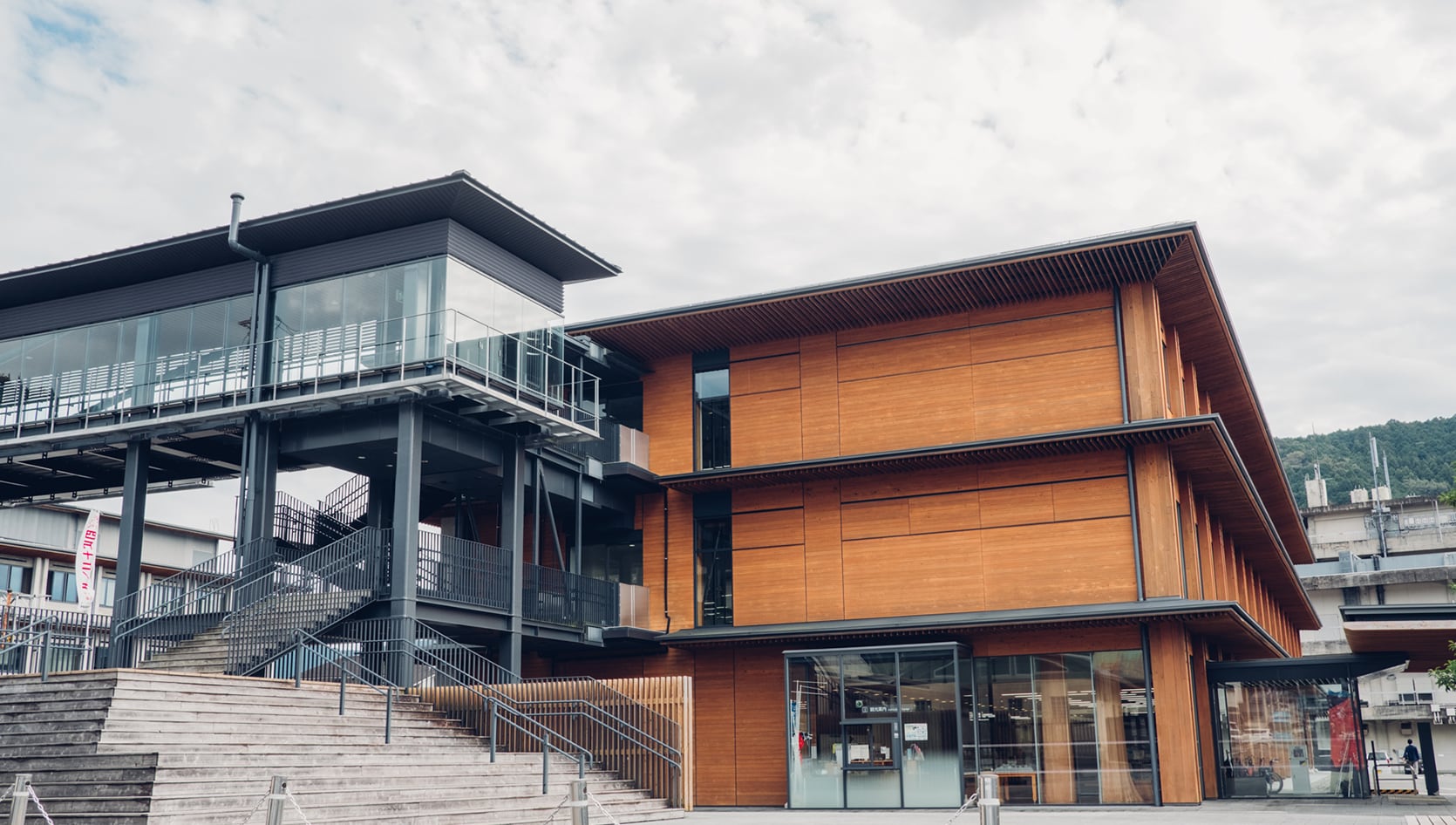
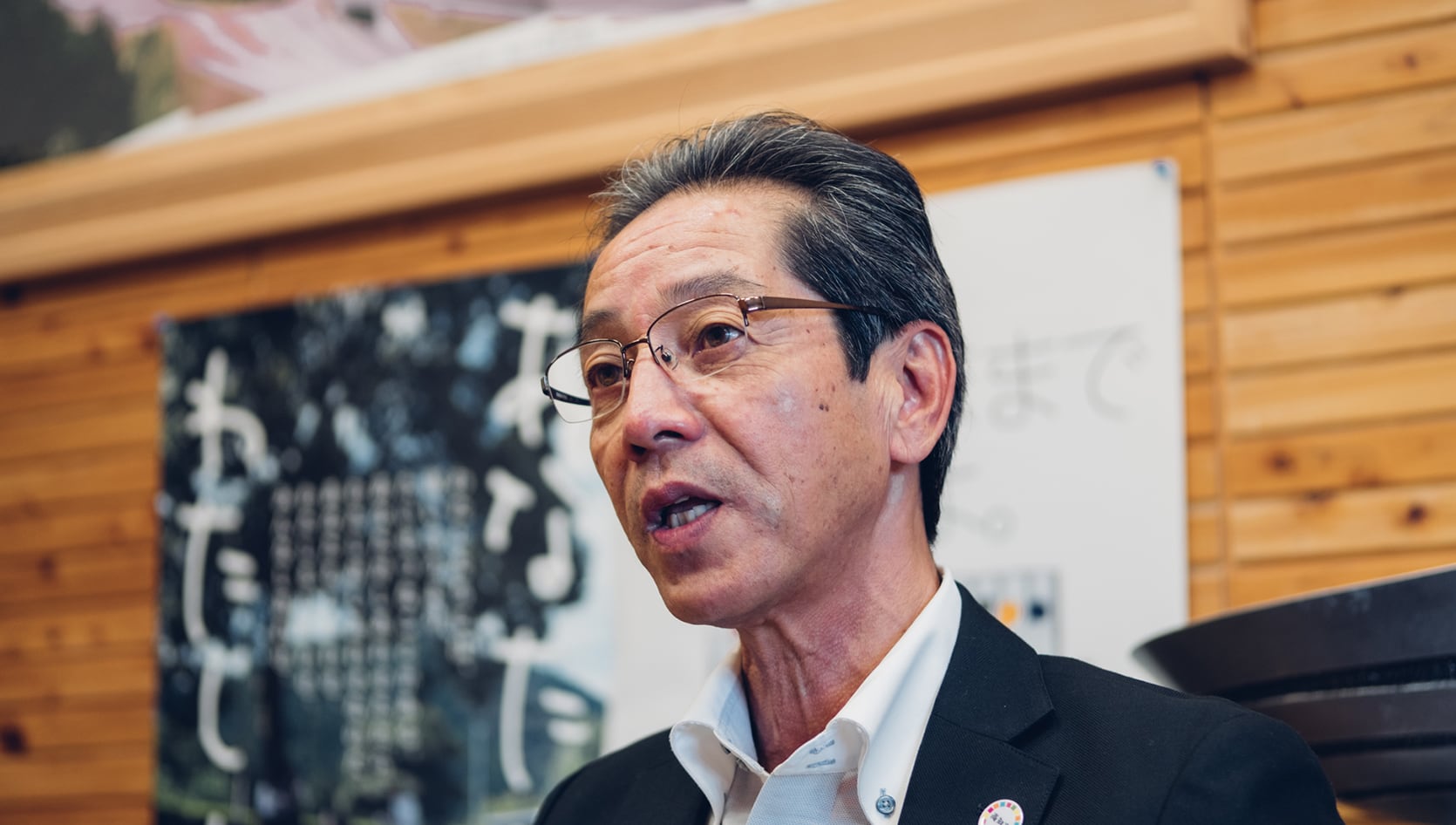
Utilizing thinned wood of the locally-owned forest.
We continue to have many tour groups come to visit the facility and learn from it. There are few buildings that make such ample use of wood from forest thinning. It has been two years since it was built, yet the color remains quite lively, and the floors are almost in perfect condition. Hardening hinoki cypress by compressing it has allowed us to use it for the floors of every story.
Generally speaking, building materials are ordered by the contractor, but in this case, the town was the one to order it. This was because of the large volume needed, the time required to dry it, and timing that to the construction start dates. That being said, we are by no means experts in construction and architecture, so the designers helped us through the order process. They kept stock of the procurement process, spoke with stakeholders, and committed to delivering results. It was quite a unique project in that respect.

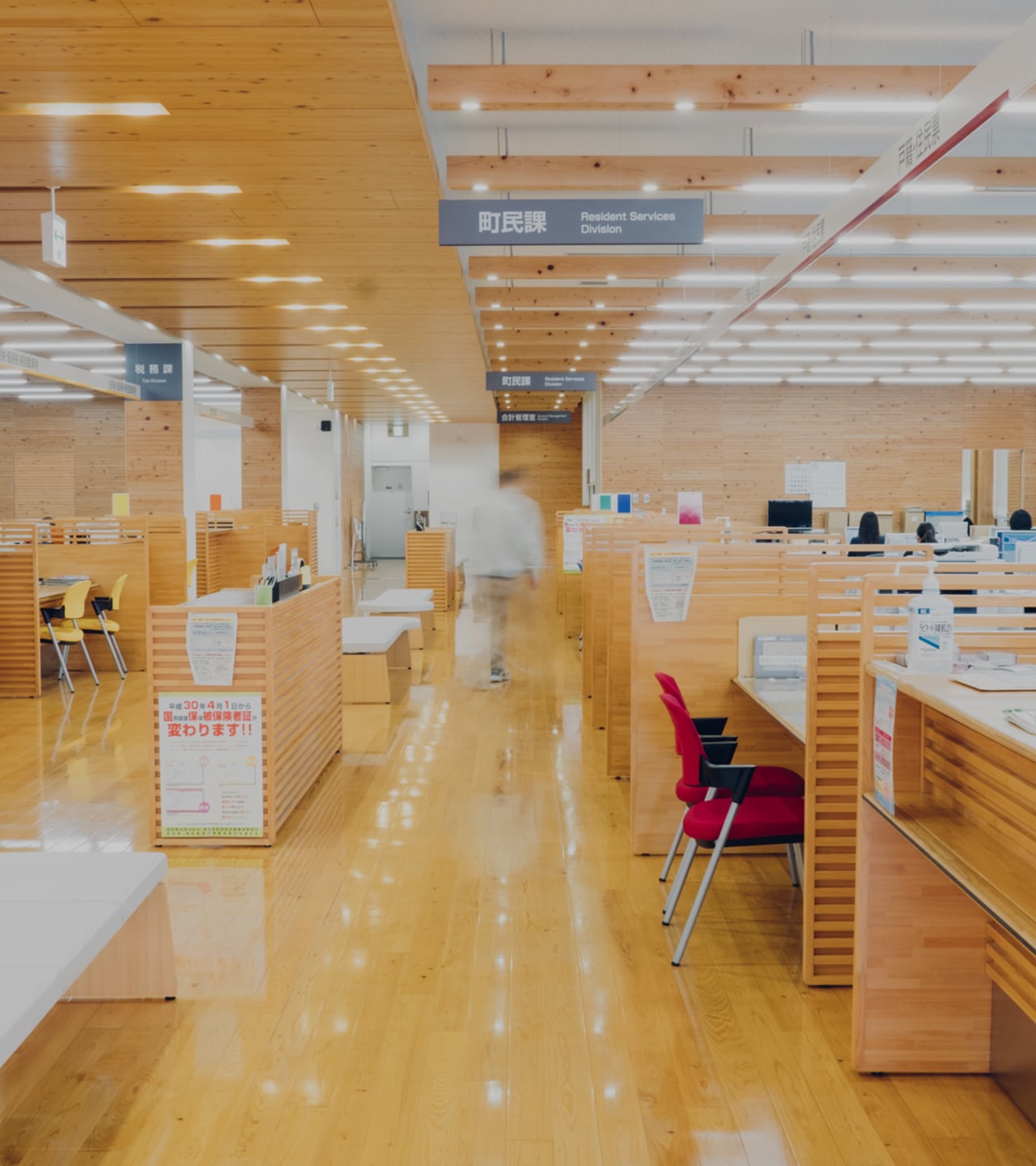
Architecture tied to the natural environment
Coexisting with nature while reaping its blessings


Making production match the natural cycle of things. Only using that which you fell, not more.
This town hall was constructed solely from thinned hinoki cypress belonging to the town and of a given thickness, and felled within that year. The design takes into account that only actual quantities of felled wood would be used. The approach is inherently about local production for local consumption, with no wood sourced in from elsewhere. This saw us applying the architectural process to the cycle of environmental preservation. Keeping forests healthy and growing requires periodically thinning them. Ensuring that the process remains economically viable requires finding ways to use the resulting thinned wood. We proposed using this lumber for the construction of the new town hall.
Creating a large space like this requires the use of thick pieces of lumber. However, thinned wood tends to not be so thick and must be laminated into larger pieces by select wood processing plants. This would produce additional transport and energy costs, however, which would hardly translate to returns for local industry. To that end, we designed a technique to bind together thinner pieces of wood using a unique bolt-based joinery system. Only one local sawmill is equipped to perform this technique.
We were consistent in designing this such that only actual quantities of lumber would be used, with nothing going to waste. That also meant compromising — wood is not used throughout, but is paired with reinforced concrete and steel where necessary. It is a hybrid design. With a railroad in between the building, the unique structure employs reinforced concrete on the railroad side and wood on the other, with beams made from steel. Reinforced concrete has better seismic resistance and sound damping. It was not merely an issue of a lack of materials, but of rationalizing the design of the entire building to imbue it with other properties. By that token, the lumber is not merely structural in nature, but was also widely used in the floors, walls, ceilings, and even desks and furniture.
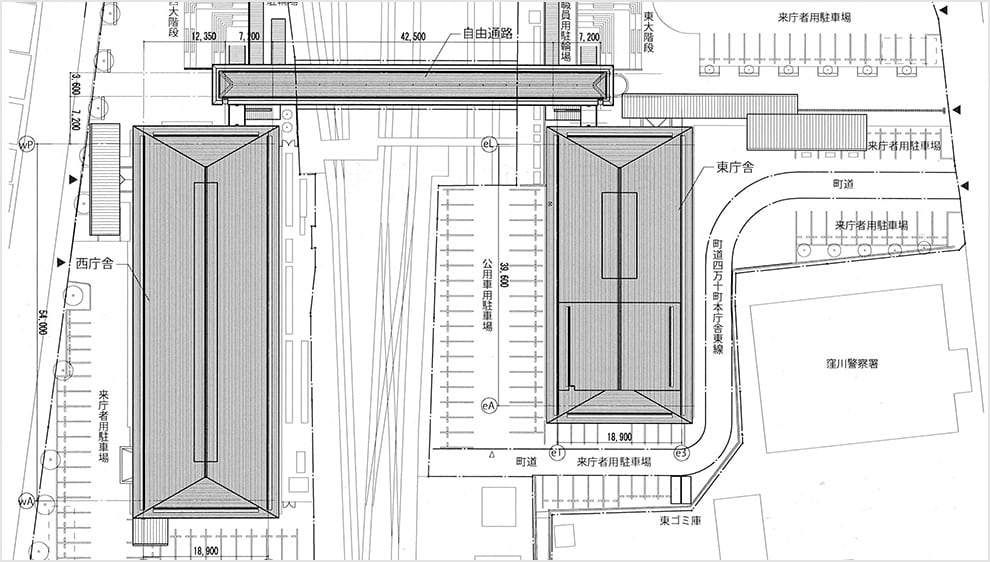
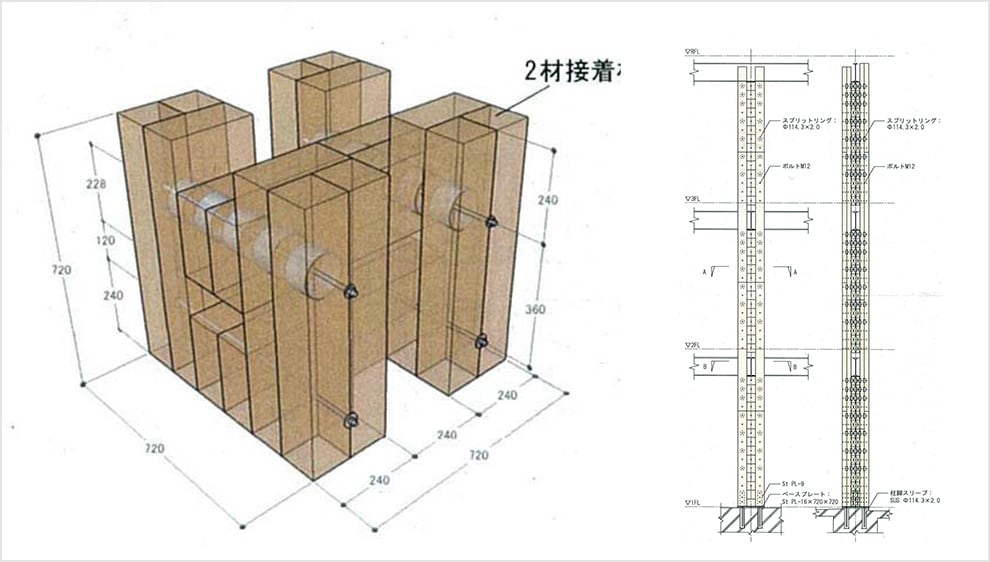
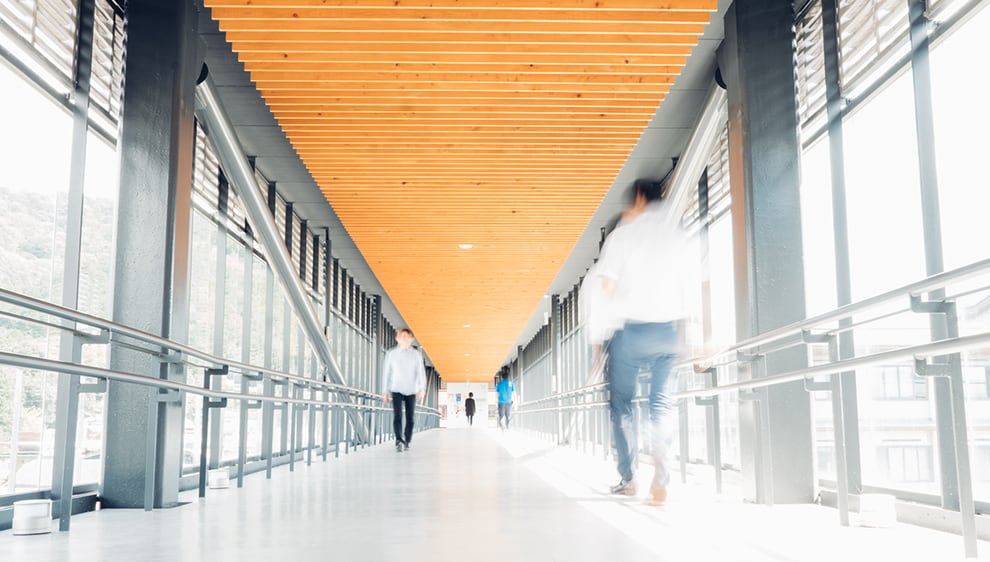

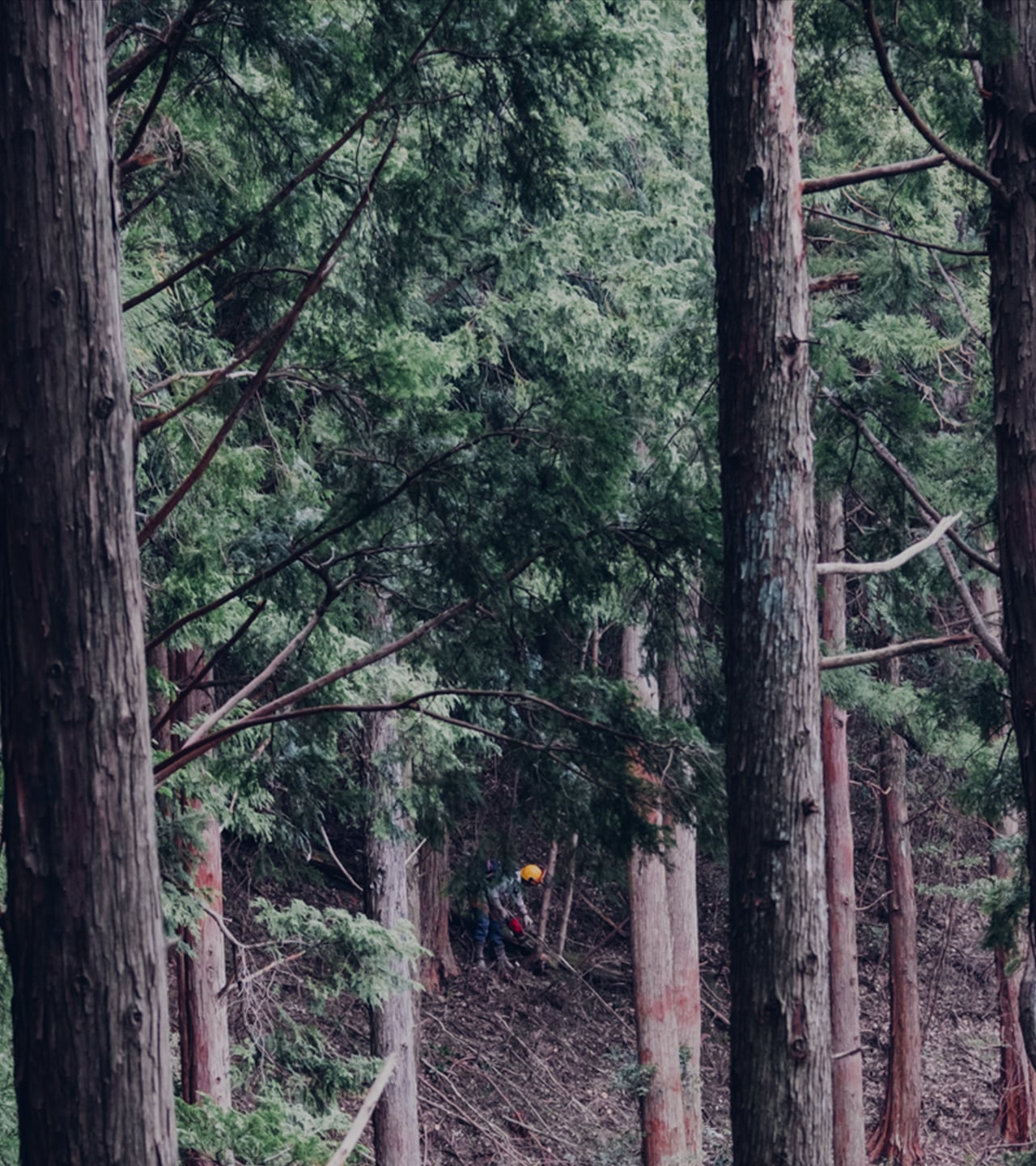
Making use of thinned wood from 40 year-old forests.
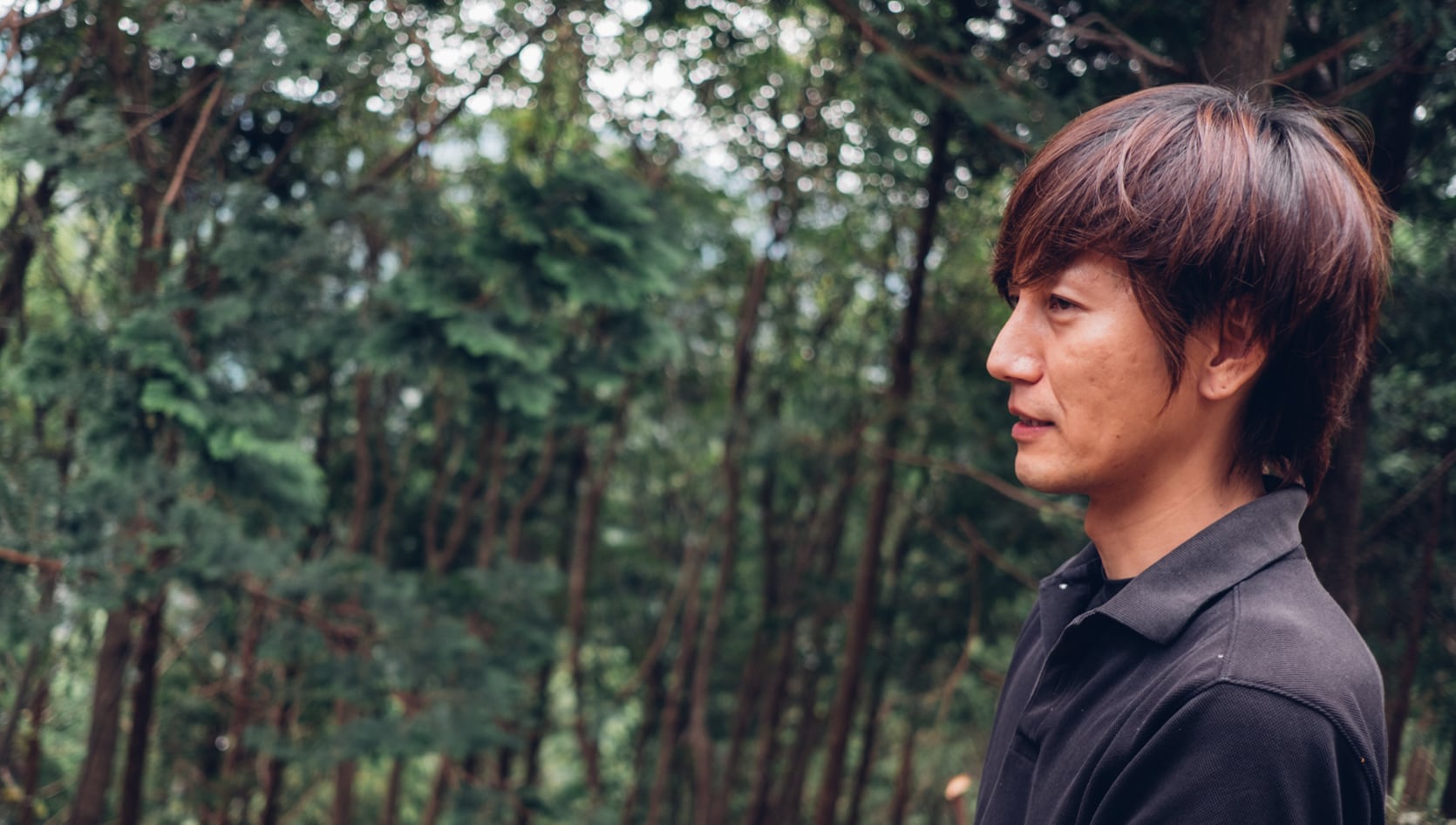
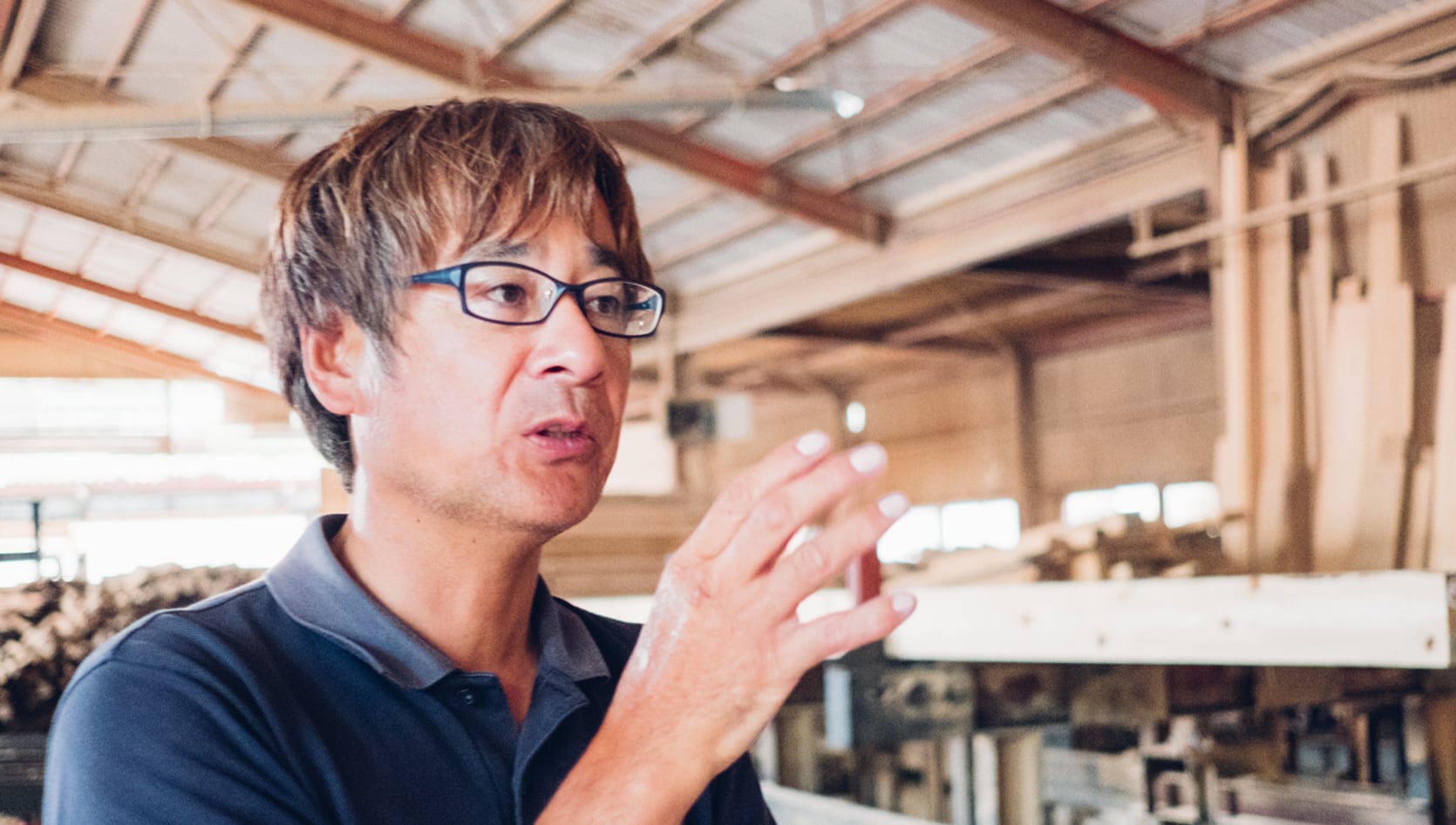
Making use of thinned hinoki cypress wood.
The Forest Association receives contracted work from owners of land in the mountains to maintain the forests growing there. Five years after afforestation, the undergrowth is trimmed. During the next 5-10 years thereafter, we thin and remove the various small trees growing around the newly-planted ones. This would be akin to weeding a plot of farmland. After twenty years, the trees grow to about 10cm in diameter. This is when we can begin first felling them. However, thinned wood at this size is sometimes used for woodchips and stakes, but when you take the transportation costs into account, it is seldom worth the expense. This is treated as scrap and left in the woods to rot, then used as humus to fortify the soil in which the trees grow. It takes a bit longer to get wood of a sufficient thickness suitable for use and shipment.
Periodic thinning is essential to properly growing the forest and keeping it from becoming unruly. It also enables the sunlight to break through the tree cover and fortify the undergrowth. If the undergrowth cannot photosynthesize, the soil becomes less moisture-retaining, which can cause trees to topple and the topsoil to run off when it rains. Thinning is also essential to creating paths through the forest when it is time to ship the wood. There are many forests in Japan where the owners skimp on proper thinning, which causes the forest to lapse into decay. There are more and more regions where, due to the influx of inexpensive imported wood, they cannot find buyers for their lumber, so the forests lapse into disrepair.
As for which trees should be felled, this is something seasoned workers decide. One in three is felled, starting with the inferior trees, then the best ones. We leave the good trees that are still in the process of developing. The trees that are markedly thicker than others mean they grew too quickly, which causes the wood grain to appear coarse. Furthermore, the wood itself is not as strong. So these are also felled. The resulting lumber is cut into 2, 3, 4, or 6 meter pieces and shipped. So it takes close to forty years to get a hinoki pillar that is 12cm square.
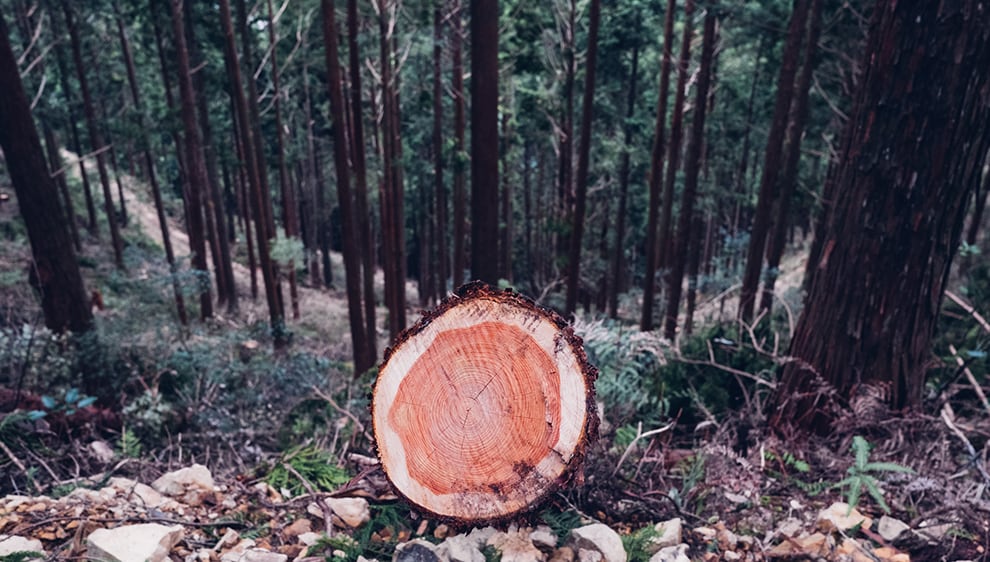

The process of sawing the wood is done locally.
The felled hinoki cypress is cut down per the following steps: First, the bark is removed. A grinder is used to peel off the bark in one fell swoop. Next, the logs are cut into square pieces. A long, flat blade is applied to a band saw or circular saw, with the logs placed on a bed and pushed through. Pushing the logs past twin band saws produces two pieces; pushing them through twice gives you four. Once the logs are cut into blocks, they are dried using an accelerated process. The lumber is placed into a dryer and heated for a week until the moisture content drops to a desired amount. After drying, a pruner, or automatic plane, is used to smooth the wood to the desired dimensions. Lastly, the durability and moisture content are mechanically tested, and the wood is graded, with seals being automatically branded on each.
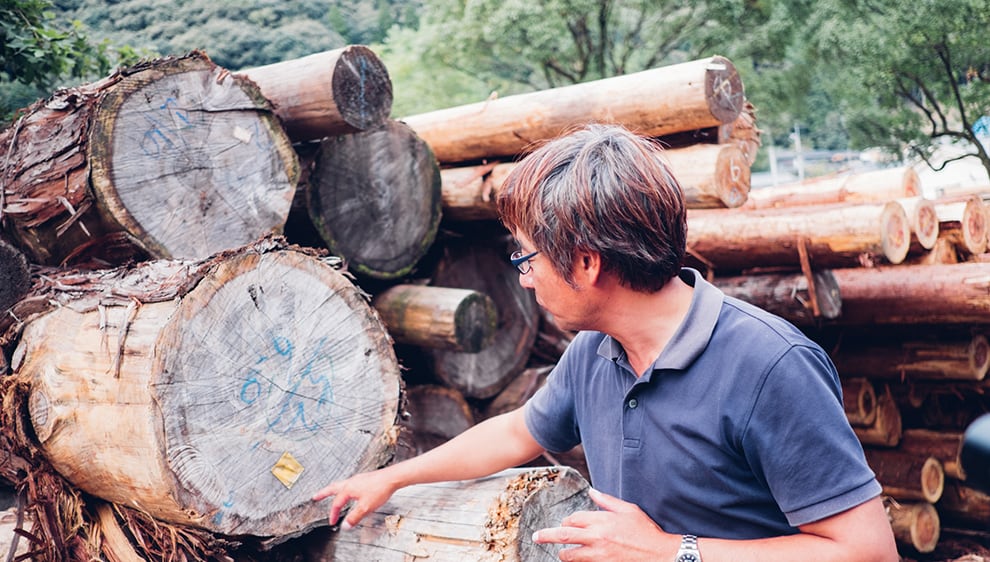
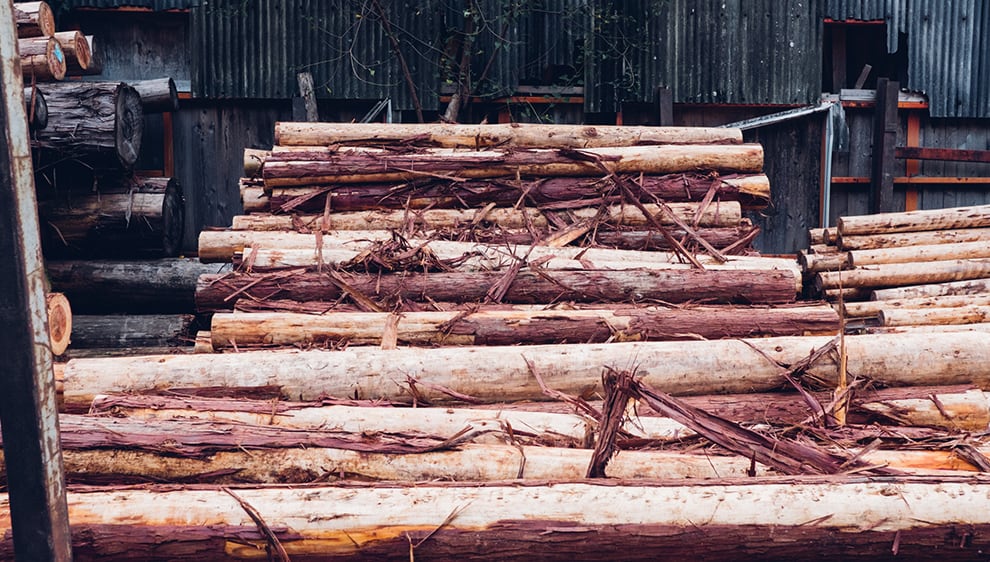
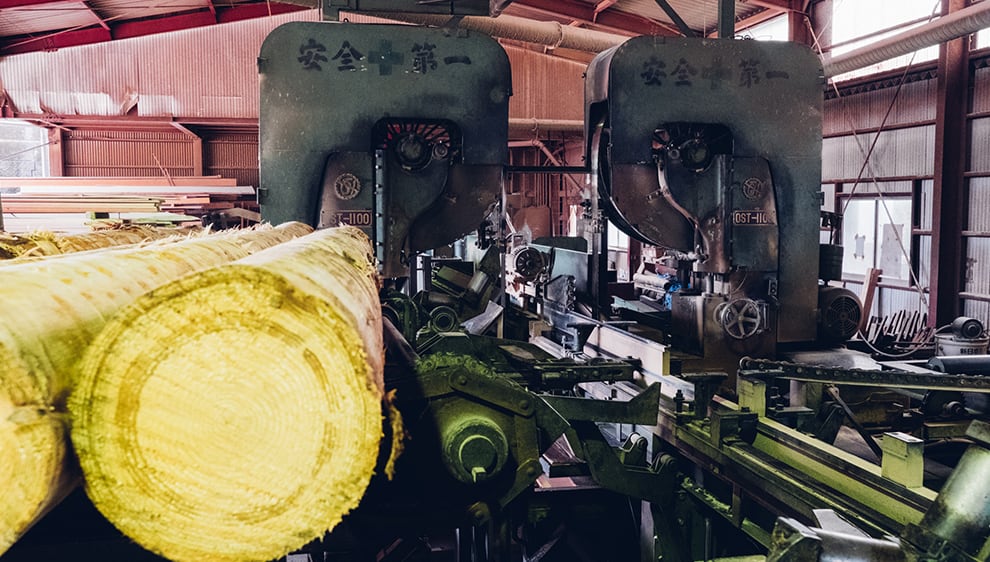
